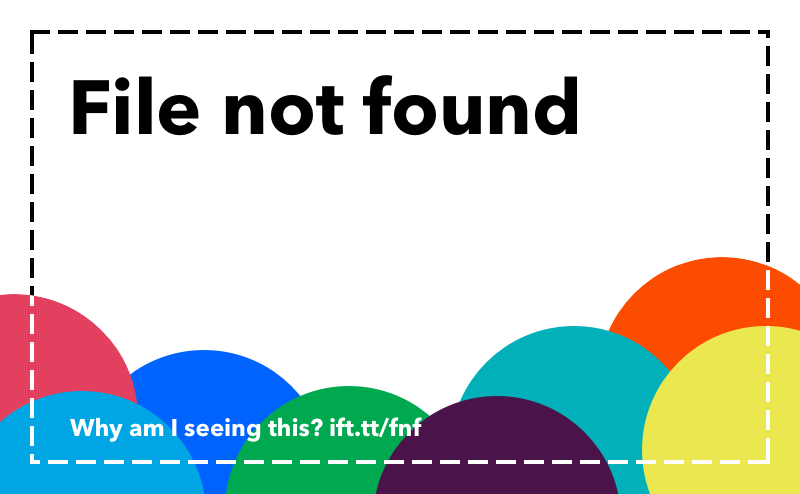
full image - Repost: 7 Machine Vision Image Acquisition Challenges (from Reddit.com, 7 Machine Vision Image Acquisition Challenges)
Mining:
Exchanges:
Donations:
Table Of Contents1. Imaging Complex Geometries2. Challenging Surfaces3. A Large Number of Variants4. Complex Material Handeling5. Working Distance Constrains6. High Resolution NecessitiesBackground of Industrial Image Acquisition Challenges:According to Fanuc, Image Acquisition contributes to 85% of Machine Vision solution success. The workflow of a typical AI based Machine Vision system includes four steps. First, the image acquisition is done through a Plug n Play camera setup that optimizes the acquisition process. Second, data preparation is done by configuring and collecting training images. Third, specialized deep learning architecture trains are used to optimize models using cloud infrastructure. Finally, the optimized model is deployed for inferencing in an edge device and monitored for accuracy. The first step of the workflow, image acquisition is a complex process and has a lot of challenges.However, a regular industrial setting comes with many challenges that make it increasingly hard to acquire perfect images for conducting visual process or quality inspectionsAlso read: Image Acquisition ComponentsLet’s look at some real world scenarios:Imaging of complex geometries –The manufacturing industry builds a lot of parts with complex geometries. These parts have multiple faces, complex shapes, and small detailing that can be seen from some angles. Such objects consist of design structures including undercuts, hollow space, or intricate internal details. To capture the images of such parts for the training of the machine vision system, the parts either need to be rotated and moved or multiple cameras need to be deployed to capture all the intricacies of the object so that defects that come in the production line can be detected with minimal errors. Challenging surfaces –Surfaces that are either transparent or reflective pose a challenge for image acquisition systems. Even in uniform lighting conditions, these surfaces cannot be captured adequately by the vision system for proper training and inspection. There have to be specialized lighting techniques so that useful training images can be taken from such surfaces. These can include dome light, diffused lighting, or any such lighting which makes sure that illumination is spread evenly across the entire surface. The use of polarised light can also reduce lighting hotspots that make it difficult to capture images.A large number of variants –In any industrial business, there are many variants of parts and materials being manufactured at a large scale. All such SKUs or stock-keeping units must be thoroughly inspected for defects. They differ in size, shape, color, geometry, and the production volume and the AI needs to comprehensively inspect them for errors. A robust cataloguing system can help the design of a good training dataset that has an even distribution of all such SKUs in terms of the errors that need to be addressed in them in the ratio of their production volumes. This avoids any bias in the training data due to unbalanced and skewed numbers. Harsh environments –The manufacturing industry has a lot of operations that have to be performed in harsh environments with dust, smoke, or heat. Some environments are also hazardous for people working in them. In harsh environments, image acquisition systems need to work and deliver results. Enclosures with correct IP ratings can protect the hardware. Other kinds of enclosures are used for explosive environments. Harsh environments can affect the hardware of the system and hazards can damage the product altogether. Continuous and correct use of protective layers over acquisition equipment safeguards the system and allows it to function correctly. Complex Material Handling – Harsh environments also affect the materials that are being inspected by the machine vision system. During inspection processes, materials should not be compromised for any reason. Sometimes, customized material handling systems need to be developed to cater to these materials. Better material handling translates into better image acquisition, and in turn higher accuracy from the machine vision system due to clarity of images. For instance, fasteners that come in bulk need to be provided feeding systems so that cameras can localize each object and take a picture at the required angle and orientation. Working Distance Constraints –Inspections of existing materials might need to be done in conjunction with other tasks that involve human workers or machine vision systems might need manual interventions at certain points of their operations. The positioning of cameras and the movement of humans must not cause any blockage for one another. There can be a minimum working distance constraint in larger factories or maximum working distance constraints in smaller, tighter spaces. Cameras need to be at a proper distance to the assembly line to inspect the parts. The usage of specialized optics can account for such working distance constraints.High-Resolution Necessities –While dealing with parts that have intricate details and designs and sub-parts that are very small and packed into the parent part, there is a necessity of using high-resolution image acquisition systems. To capture the tiny features, multiple cameras at different working distances can be used or a single high-resolution camera must be chosen. High-resolution imagery has challenges related to camera systems as traditional cameras like area scan cameras cannot support such image capture due to the smaller number of pixels. Line scan imaging is a new technology that can create high-resolution images for better visibility of features by the acquisition system. Summary –Thus, the challenges of image acquisition are numerous but they can be managed through good technology and intelligent design. Qualitas overcomes many such image acquisition challenges along with other hurdles that come in the workflow. Having Qualitas as a partner for machine vision technology can extend a company’s network of technologies, increase revenue and margins through profitable integration of machine vision into the inspection process of various parts getting manufactured, and gain an edge over the competitors with the use of advanced and up-to-date technology to automate all possible processes in the domain of manufacturing.AI in Machine Vision | Machine Vision Software | Machine Vision Case studies
Social Media Icons